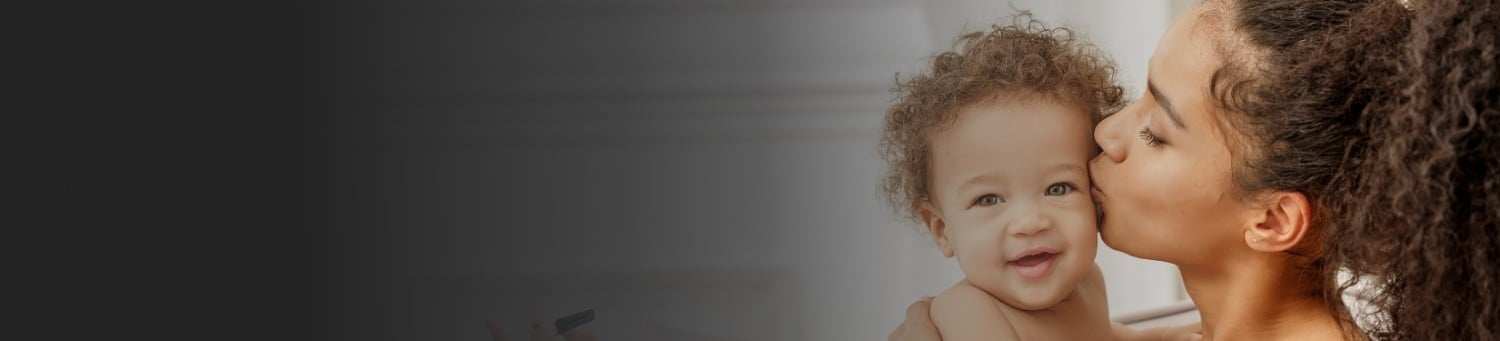
GLOBAL CONTRACT STERILIZATION SERVICES
STERIS Applied Sterilization Technologies provides contract sterilization, laboratory testing, and product and packaging testing services to medical device and pharmaceutical manufacturers.
Learn MoreOUR PRODUCTS AND SERVICES
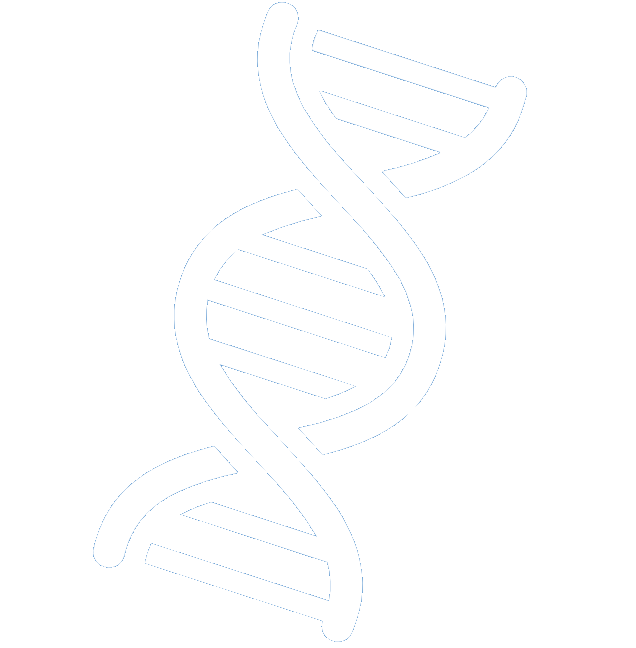
CONTRACT STERILIZATION
Global contract sterilization and microbial reduction services using a technology-neutral offering of radiation and gas technologies.
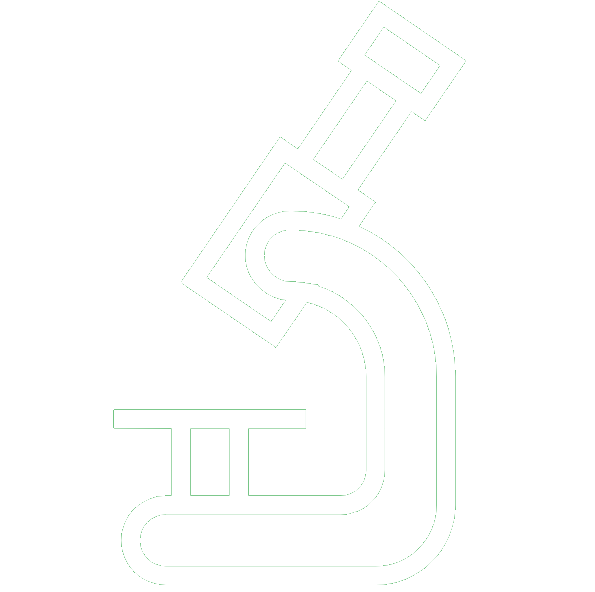
TESTING SERVICES
Testing and validation services to support the sterilization process, including microbiological, analytical, and product and packaging testing.
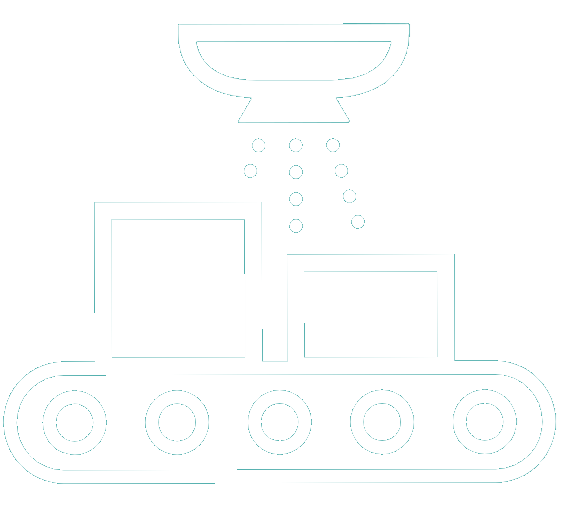
EQUIPMENT AND TECHNOLOGIES
Integrated sterilization equipment and control systems, including accelerators, conveyors, and automation.
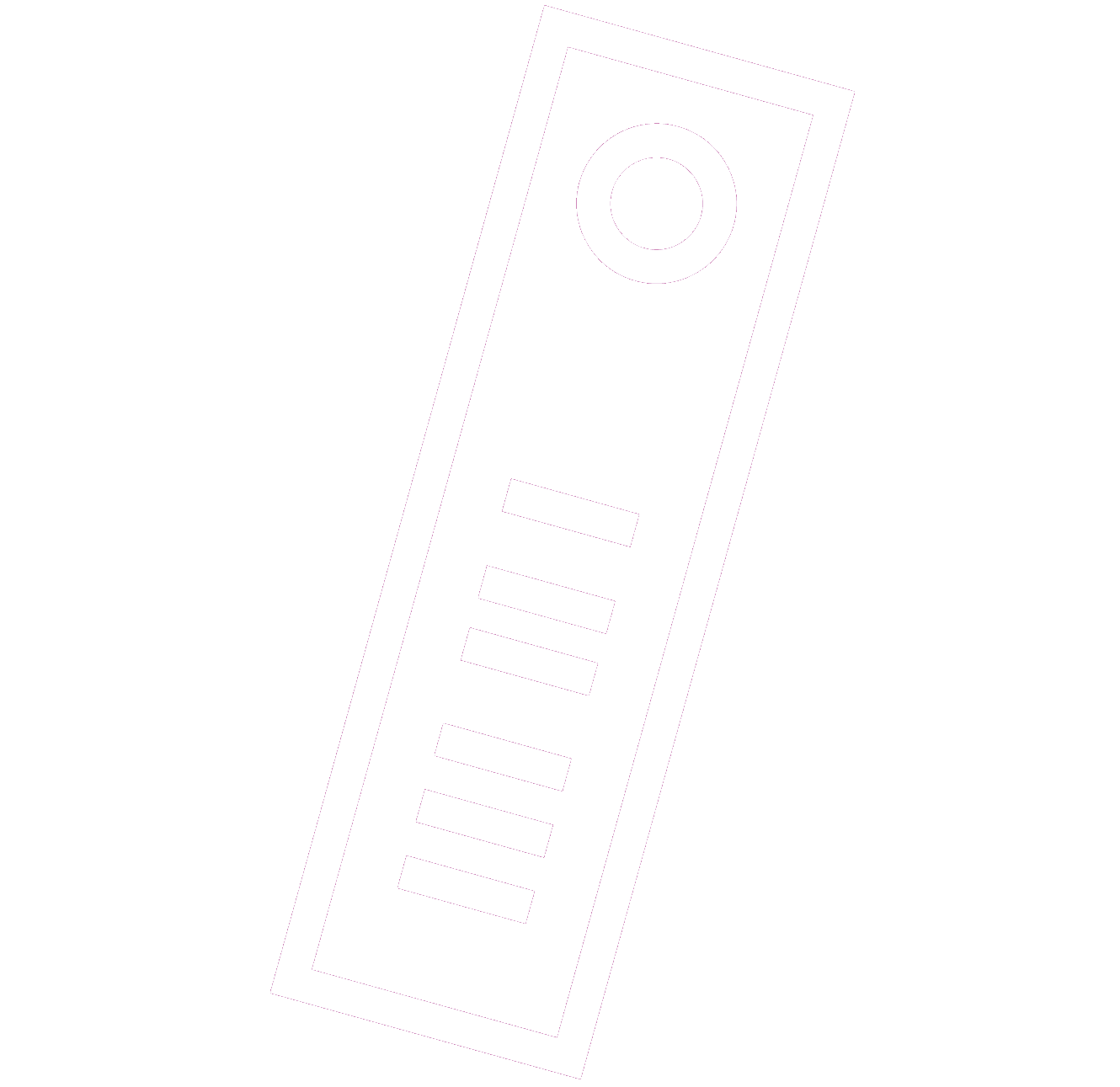
RADIATION DOSIMETRY
Supports sterilization processing with both red perspex and alanine pellet dosimeters used to measure ionizing radiation.

STERILINK®
An online interactive service that provides complete real time visibility in to STERIS processing facilites.
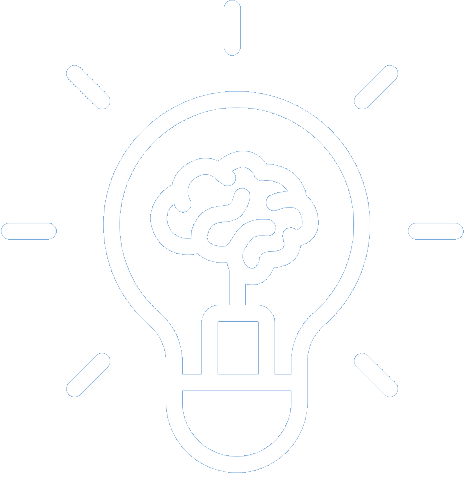
TECHTEAM® PROFESSIONALS
Our technical professionals assist in guiding our Customers through the detailed and complex sterilization and laboratory testing processes.
Recommended Resources
View our resources to learn more about sterilization and testing services.
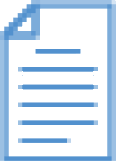
INDUSTRY ARTICLES
Articles produced in collaboration between STERIS AST and industry journals.
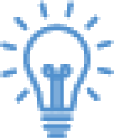
TECHTIPS
Downloadable white papers written by the STERIS AST TechTeam and other industry subject matter experts.